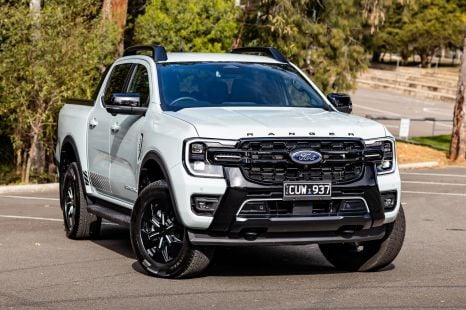
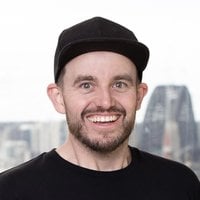
Matt Campbell
2025 Ford Ranger PHEV Stormtrak review
24 Days Ago
Contributor
Toyota has been better placed than most carmakers through the COVID-19 crisis and semiconductor shortage, but Thailand’s latest Coronavirus surge has put that in jeopardy.
A report from Nikkei Asiaclaims Toyota has put production at three of its Thai factories on hold due to a surge in COVID-19 cases.
The report says the shutdown kicked in on July 21, and will run until at least July 28. Toyota was meant to shut the factories down for the four days starting July 24 for a national holiday regardless of COVID-19.
Along with a range of cars for the south-east Asian market, the Toyota HiLux and Fortuner sold in Australia are made in Thailand.
CarExpert has contacted Toyota Australia to see if there’s any impact on the HiLux and Fortuner.
The brand is already dealing with wait times of up to three months for the ever-popular HiLux dual-cab ute, but it’s blamed inflated demand for the struggles.
“At the moment largely any delay we have in any vehicle delivery is brought about with extraordinary demand right now, we are managing that,” Toyota Australia vice president of sales and marketing, Sean Hanley, has previously told CarExpert.
The more contagious Delta COVID-19 variant is currently wreaking havoc on Thailand, which has recorded an average of almost 11,000 daily COVID cases in the last seven days.
Nikkei reports the Toyota factories were shut because COVID has impacted the supply of wire harnesses from another Thai company, which was shut after an outbreak.
Toyota hasn’t been hit as hard as some carmakers by the semiconductor shortage wreaking havoc on the global supply chain.
Speaking at the launch of the 2021 Kluger, Mr Hanley said delays in models like the RAV4 and HiLux were more to do with “extraordinary demand” than a semiconductor shortage.
“Due to forward planning, the supply of semiconductors is not the issue for Toyota as it is for other companies, particularly in Europe,” Mr Hanley said.
“Our parent company learnt a lot when its supply chain was destroyed following the 2011 Japanese earthquake and tsunami.
“As a result they now regularly examine multiple tiers of suppliers discovering at an early stage which supplies and parts are at risk.
“Our global purchasing group communicates up to 10 times a day when parts supply is severely tight and this allowed us to secure inventory for semiconductors months in advance.”
Where expert car reviews meet expert car buying – CarExpert gives you trusted advice, personalised service and real savings on your next new car.
Scott Collie is an automotive journalist based in Melbourne, Australia. Scott studied journalism at RMIT University and, after a lifelong obsession with everything automotive, started covering the car industry shortly afterwards. He has a passion for travel, and is an avid Melbourne Demons supporter.
Matt Campbell
24 Days Ago
Damion Smy
17 Days Ago
Josh Nevett
15 Days Ago
Damion Smy
15 Days Ago
William Stopford
15 Days Ago
Paul Maric
15 Days Ago