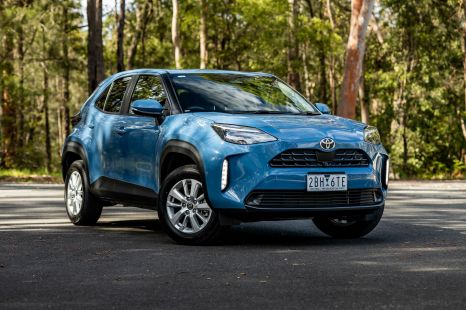
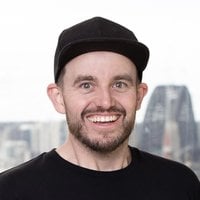
Matt Campbell
2025 Toyota Yaris Cross review
5 Days Ago
Contributor
Nissan has revealed a cleaner, greener and higher-tech new production line at its Tochigi plant that’ll soon be producing its latest electric car.
On headline aspect is the application of a new assembly technique called SUMO – simultaneous underfloor mounting operation – in which the vehicle’s powertrain is lifted into the body from underneath before robotic installation.
The Tochigi plant implementing these upgrades has begun manufacturing pre-production versions of the all-electric Ariya crossover which is scheduled for mass production by the end of Nissan’s fiscal year (March ’22).
The powertrain components used in the SUMO process are mounted all together in a plug-in style pallet.
These pallets are split up in front, middle and rear sections and are made of interchangeable modules that can accommodate layouts for electric, hybrid and internal-combustion vehicles.
Nissan says that there are currently 27 different module configurations for the plug-in pallet-style powertrains in a single facility.
During the assembly process there is real-time vehicle positioning with movement allowances of up to 0.05mm.
Currently, the company uses a less-refined mixed production method to make the all-electric Leaf hatchback.
Workers are required to guide the drivetrain components into place and manually install them.
Nissan wants to automate many of its labour-intensive processes and hand over the heavy lifting to robots.
“In Japan, there is a need to break away from conventional labour-intensive manufacturing to cope with an ageing society and serious labour shortage,” the company says in its press release.
Nissan also says it’s going ahead with this automated manufacturing process to create an improved environment for its workers so they can work more comfortably.
The SUMO assembly technique isn’t the only new technology seen in the so-called ‘Nissan Intelligent Factory’.
There are also robots that install, align and tighten suspension links, automatically install the headliner, install the cockpit module, inspect and identify vehicle flaws, as well as paint and inspect the body and bumpers.
In particular, there are 11 robots that inspect the paint of the vehicle shell and can achieve 100 per cent detection of dust and debris up to 0.3mm in diameter.
“This robot is actually replacing the human,” said a manager of the new paint shop.
“We actually transplanted human visual recognition capacity into the robot.”
The paint used in this production line is a water-based paint that cures at low temperatures allowing for the vehicle body and bumpers to be painted and baked together.
The final assembly line is littered with sensors and cameras to monitor the machines at a central control centre, where engineers can monitor for any problems.
There is also an AI that is used to predict potential breakdowns so that the robots can be fixed before anything happens.
This Intelligent Factory was first announced in 2019 with Nissan saying it would invest 33 billion yen (AU$400 million) to transform its Tochigi plant into an EV hub.
The company’s plan is for this to become a blueprint for future Nissan factory overhauls globally.
Nissan isn’t alone in upgrading its facilities with many other automakers including General Motors and Ford gearing up for their electrified futures lately.
Nissan has also committed to becoming carbon neutral with its production facilities and models globally by 2050.
“By rolling out the Nissan Intelligent Factory initiative globally, starting at the Tochigi Plant, we will more flexibly, efficiently and effectively manufacture next-generation vehicles for a decarbonised society,” said Nissan executive vice president for manufacturing and supply chain management Hideyuki Sakamto.
CarExpert helps new car buyers save thousands with expert reviews, honest advice, and transparent pricing – no dealer pressure and no sales games.
Jack Quick is an automotive journalist based in Melbourne. Jack studied journalism and photography at Deakin University in Burwood, and previously represented the university in dance nationally. In his spare time, he loves to pump Charli XCX and play a bit of Grand Theft Auto. He’s also the proud owner of a blue, manual 2020 Suzuki Jimny.
Matt Campbell
5 Days Ago
William Stopford
3 Days Ago
Josh Nevett
2 Days Ago
James Wong
2 Days Ago
Max Davies
2 Days Ago
William Stopford
1 Day Ago