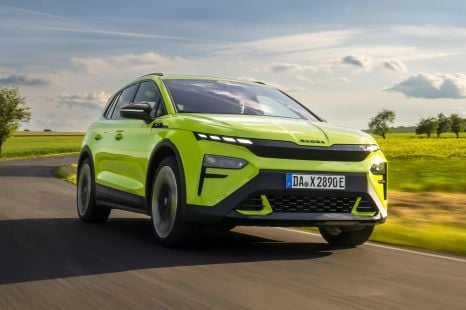
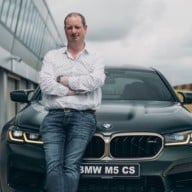
Neil Briscoe
4 Days Ago
Senior Contributor
An “environmentally promising” pilot between Audi and the Karlsruhe Instituteof Technology (KIT) to make top-shelf recycled plastic components has been completed. The next goal is to scale up production and make it cost-effective.
Plastic waste from automotive manufacturing is processed into purified pyrolysis oil, which can be used in place of petroleum as a raw material for the production of “high-quality” plastic components in Audi models through traditional means.
Chemical recycling of plastic waste could make Audi products more sustainable and eliminate greenhouse gas emissions along the supply chain.
Plastic components used in Audi’s models go beyond switches and knobs. Other components include fuel tanks, airbag covers, and radiator grilles, which must each meet stringent safety, heat resistance, and quality requirements.
Therefore, the material has to be to the right standard.
“This is why plastic automotive components that are subject to particularly high levels of stress can, to date, only be manufactured from materials of virgin material quality, which mechanically recycled plastics usually do not achieve,” Audi claims.
But recycled plastics made from pyrolysis oil are said to be of the same quality as virgin plastics.
“This means that plastics made from pyrolysis oil can be reused in automotive manufacturing to produce plastic components that are subject to high levels of stress,” the Ingolstadt-based company added.
Audi says it intends to intensify its research with the KIT and test its industrialisation potential in a follow-on project.
“An initial assessment shows that chemical recycling may be superior to energy recovery from both a financial and environmental perspective. We are comparing this process with energy recovery, as this is the current recovery route for the automotive plastic waste we analysed,” said the KIT’s Dr Rebekka Volk.
“An initial comparison of the figures shows that the costs for chemical recycling are on par with the prices that have to be paid for energy recovery. Furthermore, chemical recycling offers the opportunity to recycle much of the carbon and reuse it in the production of new plastic components.”
Audi’s project manager for chemical recycling in the supply chain, Philipp Eder, said it had the potential to give the brand a competitive edge.
“Audi wants to use intelligent methods to proactively shape the market for secondary raw materials and take responsibility in line with our mission of achieving a competitive edge through the use of innovative technologies,” he said.
Until now Audi has primarily used recycled single-variety plastics. A current example is the use of PET in the Audi A3. PET is a plastic that consists of a single-variety chemical compound. These materials are easier to process than mixed plastics.
The new Audi Q4 e-tron electric SUV contains components with recycled content – including mounting brackets, wheel arch liners, fender covers, floor paneling, and wheel spoilers.
But in the future, mixed high-performance plastics produced via chemical recycling could also be added, Audi says.
MORE: Opinion – Sustainable cabin materials should be a sexy subject
Take advantage of Australia's BIGGEST new car website to find a great deal on a Audi.
Neil Briscoe
4 Days Ago
Josh Nevett
3 Days Ago
Matt Robinson
2 Days Ago
Josh Nevett
1 Day Ago
Marton Pettendy
21 Hours Ago
James Wong
14 Hours Ago